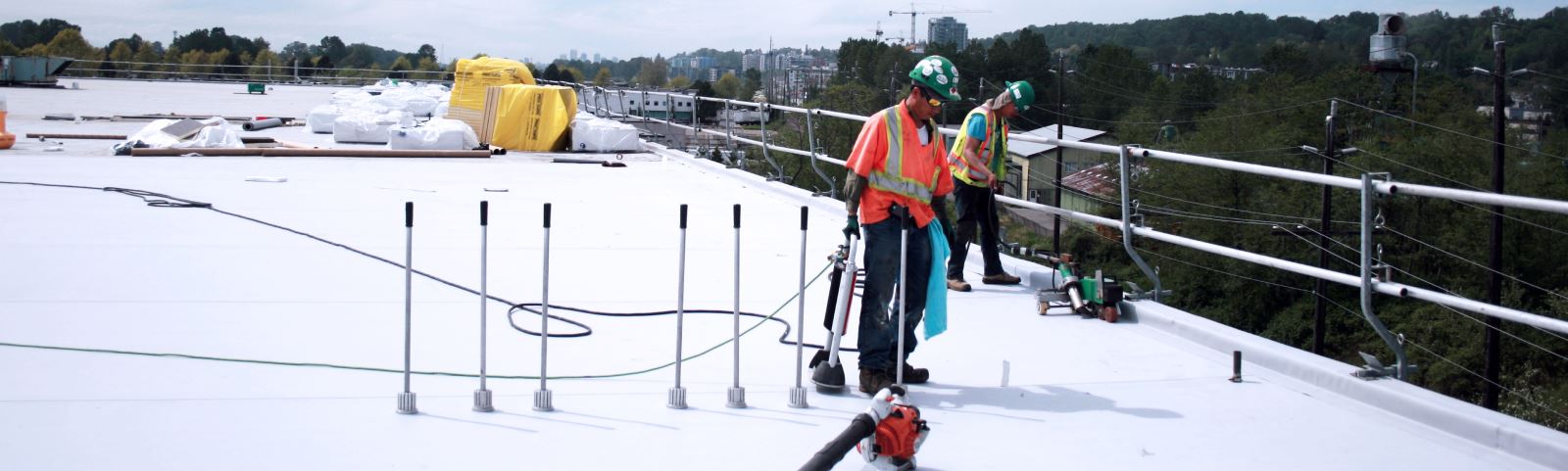
FIRESTONE RE-ROOF PROJECT
Iron Mountain Canada required a roof replacement on it's 120,000 sq. ft. facility in Burnaby, BC. Â This amounts to 15 truckloads of material to cover 2 football fields of surface area! Flynn Canada Ltd. was called in to complete the project under specific time constraints, with no interruption of business and of course no leakage - particularly due to the sensitivity of the information stored inside the building.Â
All the existing ballast (small river rock) was vacuumed off of the roof and recycled. Â Existing insulation was lifted, inspected and replaced. Â New vapor barrier was installed before reinstalling existing insulation along with a reinforcement board on top of the steel roof deck. More insulation was added on top before a new TPO roof was installed.
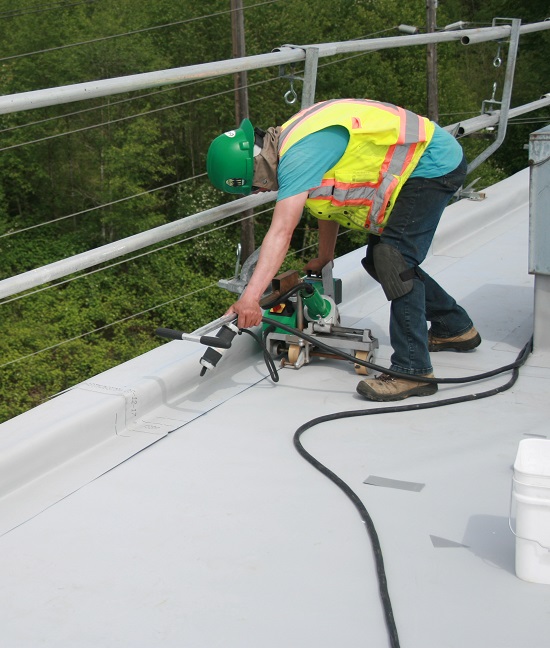
The Firestone TPO system is very fast and efficient to apply. It allows roofers to complete large areas each day. Â Without adhesives there is minimal VOC's and thus extremely environmentally friendly. Â This roof incorporates the newest ideas and the most up-to-date features in the roofing industry!
Products Used: Firestone 60 Mil Ultraply TPO in Grey, Firestone Resista, Densdeck Prime, Â 6 Mil Poly, Invisiweld Plates, Insulation Plates, Universal Pipe Flash, Unsupported Flashing, TPO Walkway, Cut Edge Sealant and Fasteners
Project Completed:Â May 1 - 25, 2018
Location:Â Burnaby, BC
Roofing Contractor:Â Flynn Canada Ltd.
Installer:Â Flynn Canada Ltd.
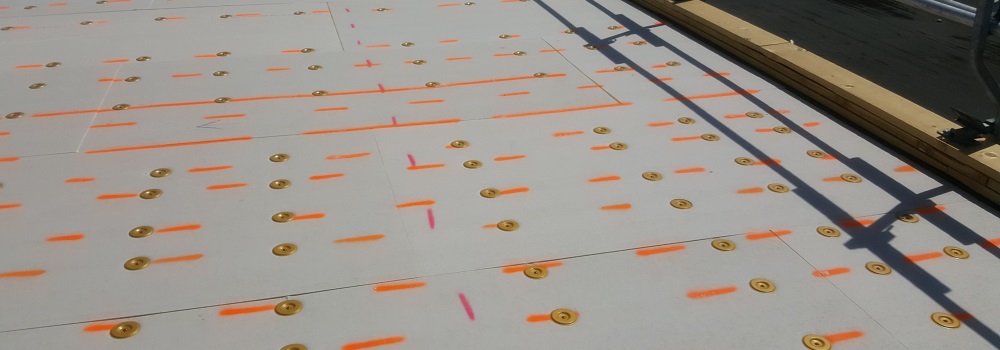
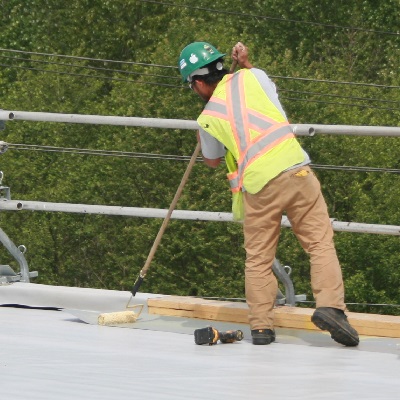
APPLYING ADHESIVE TO PERIMETER STRIP
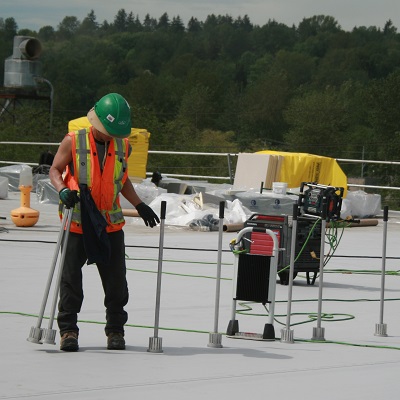
INDUCTION WELDING INVISIWELD PLATES
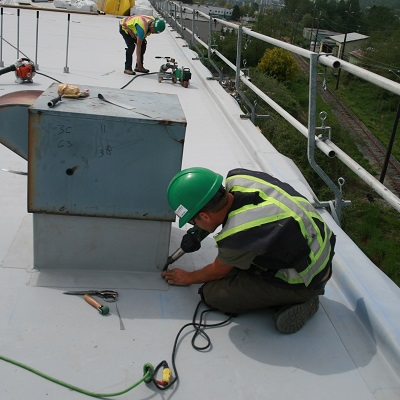
HEAT WELDING CURB DETAILS
The roofing system chosen was a complete Firestone Roofing system that allowed the roofing contractor to provide a Firestone warranty on the project to the owner. Â This system was also selected so they could use the Firestone Invisiweld system to attach the membrane to the roof without adhesives. Â
Invisiweld plates were mechanically attached with long screws to the metal roof substrate before the membrane was laid out. Â Induction welders were used to attach the membrane to the plates and the seams were welded with a robotic hot air welding machine. Â
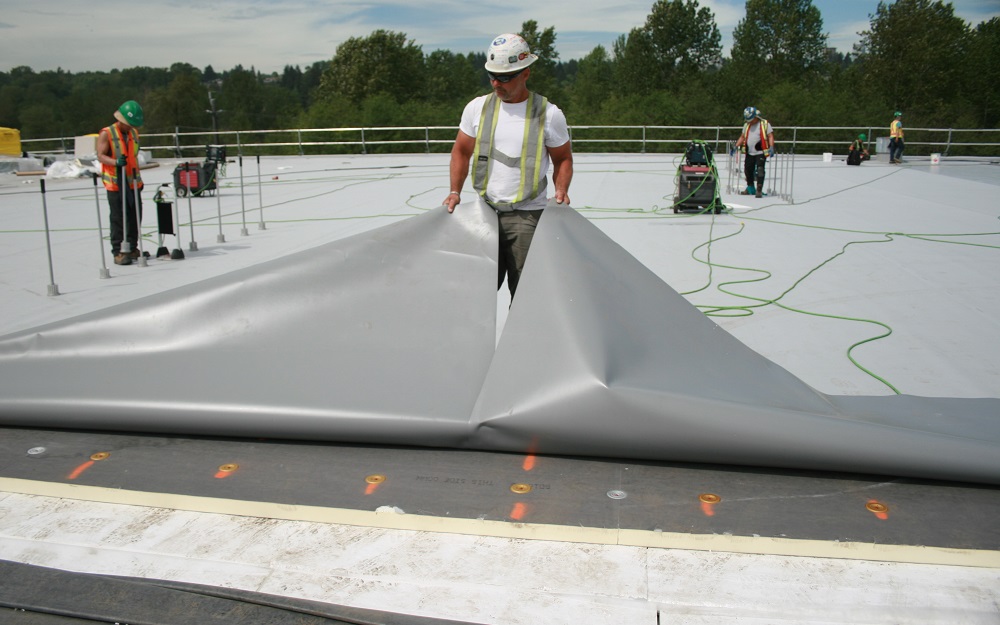